Discover the Top Reasons You Required a Chemical Defoamer for Effective Foam Control
Chemical defoamers serve as vital agents that reduce foam formation, thereby enhancing processes in fields such as food manufacturing, drugs, and wastewater therapy. As we check out the diverse advantages of chemical defoamers, it ends up being apparent that their role expands past simple foam reduction, impacting general performance in ways that may not be immediately noticeable.
Improved Functional Effectiveness
The presence of foam can impede production by blocking tools, reducing capability, and making complex procedure control. By decreasing surface area tension, they assist in the rapid collapse of foam, permitting for smoother operation and reducing downtime.
In markets such as food and drink, drugs, and wastewater therapy, the application of defoamers enhances procedure security and product top quality. As an example, in fermentation procedures, managing foam generation is vital for optimizing yield and efficiency. Furthermore, making use of defoamers can cause more reliable blending and aeration, causing improved response times and general productivity.
Moreover, when foam is efficiently controlled, it minimizes the threat of overflow and contamination, guaranteeing conformity with safety and security and quality requirements. This not just enhances operations but additionally enables far better source usage. Ultimately, the assimilation of chemical defoamers into industrial processes promotes an extra effective operations, optimizing output while preserving high-grade requirements. Thus, their role in enhancing functional effectiveness can not be overstated.
Expense Cost Savings and Resource Management
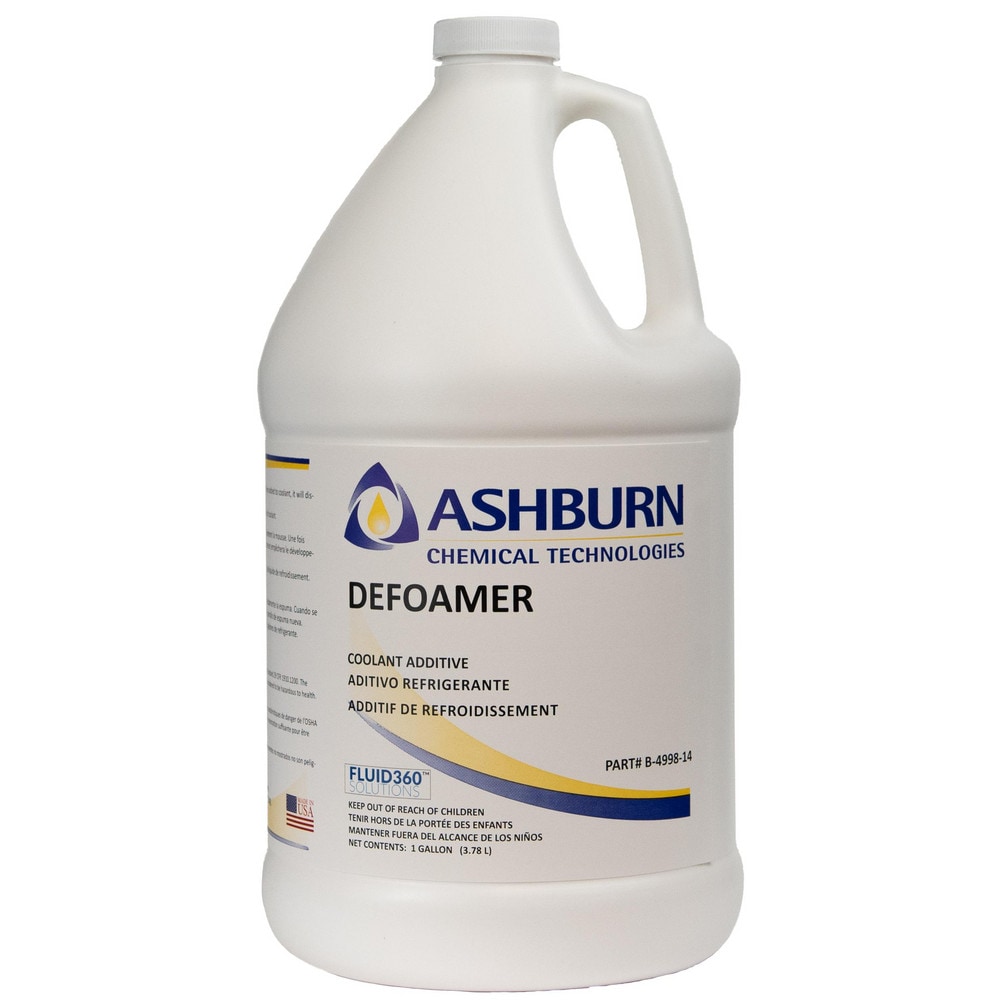
Additionally, using defoamers improves the efficiency of basic material usage. In numerous applications, excessive foam can create overuse of chemicals, causing unnecessary costs. By regulating foam degrees, organizations can optimize their chemical input, thereby lowering operational costs. This not just adds to monetary cost savings however additionally promotes sustainable practices by decreasing waste.
In addition, lowered foam in handling systems can boost the general throughput, allowing facilities to increase manufacturing ability without incurring additional costs - Chemical Defoamer. This efficient source monitoring equates into substantial financial advantages, allowing companies to assign funds toward technology or development. In summary, the combination of chemical defoamers right into commercial processes cultivates a more economical and resource-efficient atmosphere, ultimately sustaining organizational growth and sustainability
Improved Item High Quality
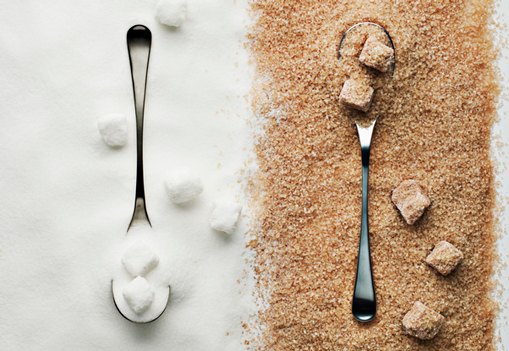
Making use of chemical defoamers plays an important role in boosting product top quality across numerous markets. Excessive foam can bring about inconsistent item formulas, influencing the final characteristics of goods such as paints, coverings, food, and pharmaceuticals. By reducing foam formation, chemical defoamers help with smoother production processes, guaranteeing that formulations remain uniform and meet specified quality standards.
In the food and beverage market, for instance, the presence of foam can affect the clarity and taste of items, inevitably influencing customer contentment. Chemical defoamers help keep the desired texture and appearance, consequently boosting the overall high quality of the end product. Likewise, in the production of paints and coverings, foam can lead to flaws such as pinholes and inadequate adhesion, weakening the item's efficiency.
In addition, making use of defoamers can enhance the efficiency of processes like fermentation and emulsification, which are essential for accomplishing preferred item features. By improving manufacturing and making certain consistent top quality, chemical defoamers not just boost the end item yet also contribute to a favorable brand track record. Hence, spending in effective foam control options is vital for any organization aiming to deliver high-quality items continually.
Equipment Protection and Longevity
Minimizing foam production is essential for protecting equipment and ensuring its long life in numerous commercial applications. Extreme foam can cause a series of functional problems, including tools damages, boosted maintenance expenses, and unplanned downtime. When foam accumulates, it can create overflow, bring about spills that endanger the stability of machinery and bordering locations.
Additionally, foam can obstruct sensors and pumps, which can hinder efficiency and performance. In serious cases, it can result in the failure of parts, requiring costly fixings or substitutes. By using a chemical defoamer, business can efficiently mitigate foam development, therefore securing their equipment from the destructive impacts of foam-related issues.
In addition to stopping damages, effective foam control can substantially enhance the operational life expectancy of equipment. Investing in a quality chemical additional reading defoamer is a positive approach for protecting devices and cultivating long life in industrial settings.
Adaptability Throughout Industries
Chemical defoamers play a critical role in different sectors, effectively dealing with foam-related difficulties across diverse applications. Their adaptability is apparent in see page industries such as food and beverage, drugs, and wastewater therapy, where foam can hamper procedures and lower efficiency. In the food industry, defoamers make sure smooth manufacturing by protecting against foam development throughout blending, fermentation, and bottling, therefore keeping item top quality and consistency.

In addition, in wastewater therapy centers, chemical defoamers are utilized to control foam throughout the aeration process, promoting optimum microbial task and enhancing the total treatment effectiveness. Their ability to work successfully in high-temperature and high-shear atmospheres further emphasizes their flexibility.
Conclusion
Finally, the use of chemical defoamers is vital for effective foam control throughout numerous industries. Their capability to enhance operational efficiency, produce substantial price savings, enhance item top quality, and shield equipment emphasizes their essential role in industrial processes. The flexibility of defoamers allows for extensive application in food production, pharmaceuticals, and wastewater treatment, ultimately contributing to sustainable growth and the maintenance of high operational criteria. The integration of defoamers is essential for enhancing total performance.
Chemical defoamers offer as necessary representatives that reduce foam formation, thus improving processes in industries such as food production, drugs, and wastewater therapy. As we discover the complex benefits of chemical defoamers, it ends up being apparent that their role expands past mere foam reduction, affecting total productivity in ways that might not be right away obvious.
By mitigating foam development, chemical defoamers assist in smoother manufacturing processes, ensuring that formulas stay uniform and fulfill given quality criteria.
By using a chemical defoamer, companies can successfully reduce foam formation, hence protecting their tools from the damaging effects of foam-related concerns.
In final thought, the usage of chemical defoamers is necessary for this efficient foam control throughout different sectors.